Trending Insights
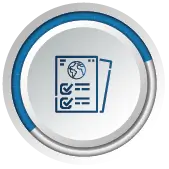
Global Leaders in Strategy and Innovation Rely on Our Expertise to Seize Growth Opportunities
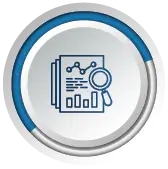
Our Research is the Cornerstone of 1000 Firms to Stay in the Lead
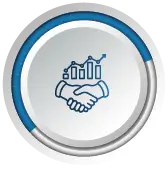
1000 Top Companies Partner with Us to Explore Fresh Revenue Channels
US Tariff Impact on Prefabricated Modular Building Market
Trump Tariffs Ignite Global Business Evolution
Request FREE sample PDF 
Pharmacy benefit management market
PREFABRICATED MODULAR BUILDING MARKET OVERVIEW
The global prefabricated modular building market, valued at USD 169.27 billion in 2024, is projected to grow steadily to USD 180.76 billion in 2025 and is expected to reach USD 305.73 billion by 2033, maintaining a CAGR of 6.79% over the forecast period.
Prefabricated modular homes are modern production solutions in which structures are constructed off-web pages in managed manufacturing unit environments and then transported and assembled in the desired area. These homes consist of standardised modules or sections that are precision engineered and may be customised to meet specific requirements. They are widely used across various sectors, which include residential housing, industrial workplaces, healthcare centres, academic establishments, and brief structures, imparting advantages like faster construction instances, cost-efficiency, reduced fabric wastage, and decreased environmental effects. Prefabrication lets in for high first-class and consistency as manufacturing takes place in controlled situations, mitigating the dangers of weather-associated delays and quality fluctuations. The modular design also complements flexibility and scalability, making it a more and more attractive solution in modern construction projects as demand for sustainable and efficient construction strategies rises globally.
COVID-19 IMPACT
"Demand for modular solutions surged due to their rapid and flexible responses to emergency needs"
The global COVID-19 pandemic has been unprecedented and staggering, with the market experiencing higher-than-anticipated demand across all regions compared to pre-pandemic levels. The sudden market growth reflected by the rise in CAGR is attributable to the market’s growth and demand returning to pre-pandemic levels.
The coronavirus chaos led to a pandemic that had an enormous twin effect on the prefabricated modular building market. Initially, the market faced demanding situations along with disrupted supply chains, exertions shortages, and restrictions on construction activities, inflicting delays in undertaking timelines and extended charges. However, because the pandemic opened up, the market witnessed a surge in demand for modular answers because of their ability to offer speedy and bendy responses to emergency wishes. Governments and healthcare organisations more and more trust prefabricated modular buildings for brief hospitals, quarantine centres, and testing facilities. Furthermore, the reduced dependency on on-website exertions and shorter creation intervals aligned properly with the social distancing necessities of the time. As a result, the pandemic highlighted the flexibility and performance of modular production, accelerating its adoption in numerous sectors post-pandemic.
LATEST TREND
"Eco friendly designs due to the integration of sustainable and smart technologies"
A key trend inside the prefabricated modular building market is the mixing of sustainable and clever technology into modular production. Builders are incorporating green substances, renewable electricity systems, and energy-green designs to align with international sustainability desires. Additionally, smart constructing technologies, together with IoT-enabled devices and automated systems for lights, heating, and security, are becoming commonplace features in modular devices. These improvements no longer most effectively decorate the functionality and appeal of prefabricated structures but additionally make contributions to reducing the carbon footprint of the development industry. The trend towards combining modular production with green and clever technologies is riding innovation inside the marketplace and making modular answers extra attractive to environmentally-conscious consumers and corporations.
PREFABRICATED MODULAR BUILDING MARKET SEGMENTATION
By Type
Based on Type, the global market can be categorized into Permanent Modular Construction (PMC) and Non-permanent Modular Construction (NPMC).
- Permanent Modular Construction (PMC): Permanent Modular Construction refers to modules which can be designed to stay in one vicinity all through their lifecycle. These systems are included in the primary building framework and meet the same requirements as traditional creation in phrases of sturdiness, safety, and aesthetics. PMC is widely used for residential, healthcare, and academic homes, in which lengthy-term infrastructure answers are required. The capability to lessen creation time by way of as much as 50%, coupled with value savings and advanced high-quality control, makes PMC a preferred choice in regions with excessive demand for sustainable and resilient infrastructure.
- Non-permanent Modular Construction (NPMC): Non-everlasting Modular Construction entails modular units which are designed for brief use and may be relocated or repurposed. This type is extensively used in programs, which include construction websites, online workplaces, occasion structures, and temporary housing at some stage in emergencies. NPMC is valued for its flexibility, ease of meeting and disassembly, and fee effectiveness in short-time period tasks. Its demand is pushed by means of sectors along with catastrophe alleviation, brief industrial areas, and mobile healthcare devices, where rapid deployment is crucial.
By Application
Based on application, the global market can be categorized into Residential, Commercial Buildings, Industrial Buildings and Others.
- Residential: The residential software segment includes modular houses, condo complexes, and low-priced housing solutions. With the developing want for quick and price-green housing, specifically in city areas, modular construction is gaining traction within the residential zone. This segment blessings from customisable designs, strength-green substances, and quicker construction timelines, addressing the housing shortages prevalent in many regions.
- Commercial Buildings: The business phase encompasses office buildings, retail spaces, hotels, and academic centres. Modular production is increasingly of favored for industrial application due to its scalability, reduced construction disruptions, and the potential to fulfil sustainability desires. High-quit tasks consisting of modular accommodations and workplace spaces emphasise aesthetics and functionality, further boosting the call for this phase.
- Industrial Buildings: Industrial packages encompass factories, warehouses, and storage facilities. The use of modular production in this section is driven by way of the want for large-scale, durable, and fast-deployable structures. Industrial homes regularly require custom-designed answers, and modular creation provides flexibility and value financial savings while ensuring compliance with protection and operational standards.
- Others: This phase covers niche packages, including healthcare facilities, instructional institutions, and leisure spaces. Modular creation is extensively used in these regions due to its ability to provide specialised systems along with cellular clinics, modular classrooms, and prefabricated sports activity complexes. The "others" category highlights the flexibility of modular construction in catering to diverse and specific infrastructure needs.
MARKET DYNAMICS
Market dynamics include driving and restraining factors, opportunities and challenges stating the market conditions.
Driving Factors
"Increasing demand with the growing urbanization and the associated demand for affordable housing"
One of the primary elements for the Prefabricated Modular Building market growth is the developing urbanisation and the associated demand for affordable housing solutions. Rapid population increase and concrete migration have led to housing shortages in lots of regions, creating a need for cost-effective and fast-deployable construction answers. Modular production addresses this challenge using supplying considerable price financial savings through decreased material waste, shorter construction timelines, and optimised hard work necessities. Governments and private developers are more and more turning to prefabricated modular buildings to fulfil housing needs successfully, mainly in densely populated urban areas, wherein traditional construction techniques can be time-ingesting and highly priced. The scalability and customisation of modular designs similarly beautify their suitability for numerous housing desires.
"Market growth with the rising demand for sustainable construction practices"
Another important aspect is the growing call for for sustainable creation practices and energy-efficient buildings. The production industry is under stress to reduce its environmental impact, and prefabricated modular homes offer a feasible answer. These systems are designed to limit material waste and electricity usage for the duration of construction, even bearing in mind the reuse or recycling of components. Modular homes can also be equipped with renewable energy systems, including sun panels, water recycling systems, and advanced insulation, making them electricity-green and environmentally pleasant. The growing adoption of green building certifications and regulations promoting sustainable creation practices is further propelling the boom of the prefabricated modular construction market.
Restraining Factor
"Budgetary constraints due to the high initial investment required"
One of the key restraining elements for the market is the high preliminary funding required for prefabrication generation and equipment. While modular construction gives price blessings ultimately, the premature expenses of specialised machinery, transportation, and skilled labour can be prohibitive for smaller construction companies or builders. Additionally, the belief that prefabricated homes are less long-lasting or aesthetically restrained in comparison to traditional structures remains a barrier in a few markets, particularly in areas with strong possibilities for conventional production. These challenges might also sluggish the adoption of modular production strategies in certain regions, mainly among rate-sensitive customers or agencies.
Opportunity
"Scope of growth with the increasing need for disaster-resilient and temporary structures"
The growing need for catastrophe-resilient and transient systems gives a big opportunity for the prefabricated modular building marketplace. Modular production is ideal for creating emergency housing, scientific facilities, and educational spaces in disaster-affected or faraway areas, thanks to its rapid deployment competencies and ease of transportation. Governments and non-governmental corporations (NGOs) are increasingly counting on prefabricated answers for catastrophe remedy and infrastructure reconstruction efforts. Moreover, as climate-associated occasions, including floods, hurricanes, and wildfires, turn out to be more common, the call for flexible and robust modular structures is expected to push upward, developing growth possibilities in this area of interest section of the market.
Challenge
"Difficulty in meeting local standards leads to compatibility issues"
A large mission for the prefabricated modular building marketplace is the shortage of standardised policies and constructing codes across distinctive areas. Modular construction processes and substances regularly need to satisfy neighbourhood standards that could range extensively and result in compatibility issues or elevated charges. This loss of uniformity complicates the scaling of modular answers throughout international markets and can discourage capacity adopters. Additionally, they want to move prefabricated modules to construction sites, which can be logistically hard, especially in areas with insufficient infrastructure, including task complexities. Addressing those regulatory and logistical challenges might be essential for the considerable adoption of modular creation.
PREFABRICATED MODULAR BUILDING MARKET REGIONAL INSIGHTS
-
North America
The prefabricated modular building market in the United States Prefabricated Modular Building market, particularly in the United States, is experiencing an extensive boom driven by the growing demand for price-effective, sustainable, and time-efficient production solutions. In the U.S., prefabrication is increasingly being followed in sectors including healthcare, training, and commercial workplace areas due to its potential to fulfil tight construction closing dates and provide splendid structures. The push for sustainable production practices and the adoption of advanced technology, such as Building Information Modeling (BIM), is similarly riding the marketplace boom. Additionally, authorities’ tasks selling inexperienced constructing certifications and catastrophe-resilient infrastructure are bolstering the call for modular creation within the place. However, no matter the developing adoption, the market faces challenges, which include logistical complexities and resistance from traditional production stakeholders. North America remains a key market, with the U.S. Gambling a pivotal function due to its emphasis on innovation and huge-scale infrastructure tasks.
-
Europe
Europe represents a mature marketplace for prefabricated modular buildings, pushed with the aid of stringent environmental guidelines, excessive exertion fees, and the need for power-green construction practices. Countries, including Germany, the United Kingdom, and Sweden, are at the leading edge of modular production adoption, leveraging superior technology and sustainable constructing materials to align with their carbon neutrality desires. The vicinity's desire for off-site production strategies is also supported by a professional staff and well-developed transportation infrastructure, permitting efficient meeting of modular gadgets. In the United Kingdom, modular production is broadly applied for public housing initiatives and healthcare facilities, whilst Scandinavian international locations have an awareness of sustainable designs and power-green modular homes. However, the market in Europe is restricted with the aid of varying building codes and requirements across nations, which may preclude large-scale implementation. Despite these challenges, Europe remains a dominant area within the worldwide marketplace because of its early adoption and sturdy consciousness of sustainability.
-
Asia
The prefabricated modular construction market in Asia is witnessing fast expansion, pushed by urbanisation, populace growth, and the growing want for low-cost housing and infrastructure. Countries like China, India, and Japan are the main marketplaces, with China dominating because of its large creation area and authorities-led tasks to sell modular answers in urban improvement projects. In India, the demand for modular buildings is fueled by the authorities’s push for inexpensive housing underneath schemes like "Housing for All," coupled with the rising adoption of sustainable production practices. Japan, however, emphasises precision engineering and fantastic modular houses tailor-made to particular wishes, leveraging advanced robotics and automation in production. However, the market in Asia is likewise characterised by challenges inclusive of constrained consciousness in certain regions and ranging degrees of industrialisation throughout nations. Asia is emerging as the dominant region inside the worldwide prefabricated modular constructing market due to its big-scale tasks, growing investments, and growing cognisance of present-day production technology.
KEY INDUSTRY PLAYERS
"Key Industry Players Shaping the Market by Addressing Industry challenge"
Key gamers in the prefabricated modular building market are instrumental in driving innovation, increasing marketplace reach, and addressing industry challenges. They make investments closely in research and development to improve construction strategies, broaden sustainable materials, and combine smart technology into modular devices. These organisations often collaborate with governments, NGOs, and private builders to sell modular answers via huge-scale initiatives and public-private partnerships. Furthermore, key players’ consciousness on instructing stakeholders about the benefits of modular production, together with fee-efficiency, speed, and sustainability, to triumph over misconceptions and increase adoption. Their efforts in marketing, technology, and strategic collaborations ensure the continuing boom and evolution of the market.
List of Top Prefabricated Modular Building Companies
- Red Sea Housing Services (Saudi Arabia)
- Laing O'Rourke (U.K.)
- Skanska AB (Sweden)
- Katerra (U.S.)
- Guerdon Modular Buildings (U.S.)
- Lendlease Corporation (Australia)
- NRB Modular Solutions (Canada)
- Algeco Group (France)
KEY INDUSTRY DEVELOPMENT
November 2024: Skanska AB released a modular workplace building mission in Sweden aimed at accomplishing net-0 carbon emissions. The undertaking integrates advanced strength-saving technology and uses recyclable substances, setting a benchmark for sustainable commercial creation. This improvement underscores the developing consciousness of green and energy-green modular construction answers.
REPORT COVERAGE
The study encompasses a comprehensive SWOT analysis and provides insights into future developments within the market. It examines various factors that contribute to the growth of the market, exploring a wide range of market categories and potential applications that may impact its trajectory in the coming years. The analysis takes into account both current trends and historical turning points, providing a holistic understanding of the market's components and identifying potential areas for growth.
The Prefabricated Modular Building market is poised for a continued boom pushed by increasing health recognition, the growing popularity of plant-based diets, and innovation in product services. Despite challenges, which include confined uncooked fabric availability and better costs, the demand for gluten-unfastened and nutrient-dense alternatives supports marketplace expansion. Key industry players are advancing via technological upgrades and strategic marketplace growth, enhancing the supply and attraction of Prefabricated Modular Building. As customer choices shift towards healthier and numerous meal options, the Prefabricated Modular Building market is expected to thrive, with persistent innovation and a broader reputation fueling its destiny prospects.
REPORT COVERAGE | DETAILS |
---|---|
Market Size Value In |
US$ 169.27 Billion in 2024 |
Market Size Value By |
US$ 305.73 Billion by 2033 |
Growth Rate |
CAGR of 6.79% from 2024 to 2033 |
Forecast Period |
2025-2033 |
Base Year |
2024 |
Historical Data Available |
Yes |
Regional Scope |
Global |
Segments Covered | |
By Type
|
|
By Application
|
Frequently Asked Questions
-
What are the driving factors of the Prefabricated Modular Building market?
The growing urbanisation and the rising demand for sustainable construction practices are the two driving factors of this Prefabricated Modular Building market.
-
What are the key Prefabricated Modular Building market segments?
The key market segmentation, which includes, based on type, the Prefabricated Modular Building market is Permanent Modular Construction (PMC) and Non-permanent Modular Construction (NPMC). Based on application, the Prefabricated Modular Building market is classified as Residential, Commercial Buildings, Industrial Buildings and Others.
-
What value is the Prefabricated Modular Building Market expected to touch by 2033?
The Prefabricated Modular Building Market is expected to reach USD 305.73 billion by 2033.
-
What CAGR is the Prefabricated Modular Building Market expected to exhibit by 2033?
The Prefabricated Modular Building Market is expected to exhibit a CAGR of 6.79% by 2033.