Trending Insights
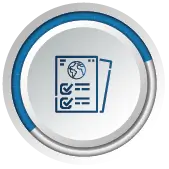
Global Leaders in Strategy and Innovation Rely on Our Expertise to Seize Growth Opportunities
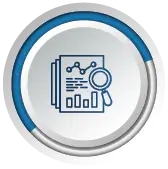
Our Research is the Cornerstone of 1000 Firms to Stay in the Lead
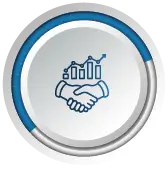
1000 Top Companies Partner with Us to Explore Fresh Revenue Channels
US Tariff Impact on Workholding Devices Market
Trump Tariffs Ignite Global Business Evolution
Request FREE sample PDF 
Pharmacy benefit management market
WORKHOLDING DEVICES MARKET OVERVIEW
The global workholding devices market size expanded rapidly in 2025 and is projected to grow substantially by 2033, exhibiting a prodigious CAGR during the forecast period.
The marketplace for workholding devices increases due to rising production requirements for precision manufacturing processes in automotive segments alongside aerospace production as well as electronics manufacturing and heavy machinery operations. Workholding devices consisting of clamps alongside chucks and vises and jigs and fixtures function as essential components for securing workpieces throughout machining operations so they remain accurate and safe while being repeatable. Using advanced workholding systems manufacturers now invest to enhance their productivity rates and speed up their setup procedures and make their processes more efficient in CNC machining operations. Intelligent workholding systems developed from smart manufacturing and Industry 4.0 technologies combine sensors with real-time monitoring to improve their performance output.
Schunk and Röhm along with Destaco and Jergens and Kitagawa operate as major market players who continue to develop customized modular workholding systems. The Asia-Pacific region controls the market because China and India are rapidly industrializing their manufacturing sectors across the region. North America and Europe also hold significant shares due to their advanced automotive and aerospace industries. The market for workholding devices will experience additional growth because automation investments are rising and engineers require high-precision machines. Market expansion in this sector faces barriers from high startup expenses along with the requirement of experts who can operate complicated systems.
COVID-19 IMPACT
"Workholding devices Industry Had a positive Effect Due to accelerated the adoption of automation and Industry 4.0 during COVID-19 Pandemic"
The COVID-19 pandemic caused diversified market effects on workholding devices through disruptions within worldwide manufacturing systems and supply network operations. The pandemic caused decreases in workholding solution demand because of lockdown procedures combined with worker shortages and short facility closure events in automotive production along with aerospace and electronics manufacturing facilities. The market experienced reduced production capacity due to supply chain disruptions that caused delays in material acquisition as well as distribution problems. The majority of small and medium enterprises made up market segments that confronted financial obstacles preventing them from spending money on updated machining and workholding solutions.
The pandemic speeded up the incorporation of automation together with Industry 4.0 manufacturing technologies into production operations which opened new chances for innovative workholding solutions. A need arose in industries to deploy automated workholding systems with sensors for remote monitoring and predictive maintenance due to their implementation of safety protocols and reduced human factory participation. Industries started their operations again after economic recovery by prioritizing efficiency and cost reduction initiatives which led to a surge in demand for innovative precise workholding solutions. The workholding devices market will become technologically advanced and more resilient since COVID-19 has created long-term impacts.
LATEST TREND
"Integration of smart and automated workholding solutions to Drive Market Growth"
The workholding devices market now features sophisticated automated workholding solutions as one of its current industry trends. The advancement of Industry 4.0 together with smart manufacturing has caused businesses to select workholding systems which feature sensors connected to IoT networks for monitoring real-time data. The advanced system provides functional benefits for predictive maintenance while decreasing setup durations and allowing better process optimization through real-time force and vibration and temperature readings. These workholding solutions improve both precision and efficiency and help reduce downtime so they benefit manufacturers seeking high accuracy automation in sectors like aerospace along with automotive fields and electronics manufacturing.
WORKHOLDING DEVICES MARKET SEGMENTATION
By Type
Based on Type, the global market can be categorized into Milling/Drilling Workholding, Turning Workholding, Grinding Workholding and EDM Workholding
- Milling/Drilling Workholding: Workpieces achieve precision stability through workholding devices that secure them during milling and drilling machining operations. The list of workholding devices includes vises also includes clamps as well as fixtures and modular workholding systems which stop components from moving under cutting forces. The solutions used in workholding improve both accuracy and vibration control to support efficient multi-axis machining operations.
- Turning Workholding: The process of turning workholding enables lathe operations where cutting tools form the workpiece through its rotation. Different workholding solutions such as mandrels, collets, faceplates, chucks provide stable and concentric material positioning. The compatibility of pneumatic and hydraulic chucks generates better performance and predictable results while processing CNC turning components.
- Grinding Workholding: The main function of workholding systems in grinding operations is to offer exact placement alongside stability for pieces during surface and cylindrical and centerless grinding applications. Workpiece stability and precision improvement come from using magnetic chucks together with vacuum chucks and v-blocks. The devices perform essential roles in manufacturing operations by allowing producers to achieve precise tolerances and maintain superior surface finish quality.
- EDM Workholding: The design of electrical discharge machining workholding systems makes sure workpieces stay secured and permits dielectric fluid together with spark erosion to flow freely. The industry uses magnetic clamps together with zero-point fixtures combined with precision vises to ensure both stability and precision in manufacturing processes. The implementation of dedicated setups lowers electrode deterioration and increases machining speed.
By Application
Based on application, the global market can be categorized into Automotive, Heavy Industrial, Aerospace and Others
- Automotive: Workholding systems within automotive manufacturing operations guarantee correct machining results for automobile engines and transmissions together with their framework components. Production speed and accuracy improve substantially through CNC machining because of hydraulic and pneumatic chucks and vises and modular fixtures. Robotic workholding solutions together with automation technologies have become essential for improving production speed and minimizing cycle times.
- Heavy Industrial: Workholding devices intended for heavy industrial applications handle the machining requirements of large heavy items including turbines as well as construction equipment and metal structures. High-force machining demands require custom fixtures together with large clamps as well as magnetic chucks to provide stable support. Structural solutions from manufacturers enable them to preserve strict dimensional precision standards while boosting industrial output levels in harsh operating settings.
- Aerospace: Machining operations within aerospace applications demand high precision because they involve vital components such as turbine blades and airframe structures and landing gear. Vacuum chucks joined with zero-point clamping systems along with adaptive fixtures enable manufacturers to reach high accuracy and repeatability levels. Advanced workholding systems allow multi-directional machining operations which reduces deformation in light materials that include titanium and composites.
MARKET DYNAMICS
Driving Factor
"Growth in CNC Machining and Automation to Boost the Market"
A factor in the workholding devices market growth is the Growth in CNC Machining and Automation. The market demand for workholding devices increases primarily because of mounting use of computer numerical control (CNC) machines and automated manufacturing systems. Today's CNC machines need precise and efficient workholding solutions which lead to accurate results along with repeated operations and speed up production processes. Manufacturing efficiency increases because automated workholding devices including hydraulic and pneumatic chucks and zero-point clamping systems and robotic fixtures reduce setup times along with improving operational efficiency.
"Expanding Aerospace and Automotive Industries to Expand the Market"
The aerospace sector together with automotive production requires precision machining to manufacture components such as engine parts as well as transmission systems and structure elements. Manufacturers depend on workholding devices to meet precision specifications which are essential for important applications. Specialized workholding solutions receive growing demand since lightweight vehicles and advanced aerospace components require increasing global demand.
Restraining Factor
"Compatibility Issues with Diverse Machining Setups to Potentially Impede Market Growth"
The compatibility issues between workholding devices and different types of machining centers create problems for their standardization and integration. Manufacturers have to spend money on tailor-made or modular workholding systems that may involve long development periods. Twelve industries collectively fail to achieve mass workholding solution deployments due to their diverse approaches across different machines.
Opportunity
"Integration of AI and IoT in Workholding Devices To Create Opportunity for the Product in the Market"
Smart workholding solutions using AI and IoT technology will define the path for the workholding devices market's development during future years. Real-time monitoring alongside predictive maintenance and automated adjustments enabled by these systems gives manufacturers improved efficiency alongside reduced downtime. Manufacturers who implement Industry 4.0 technologies will allocate funds to develop smart data-based workholding systems because these solutions boost production accuracy and operational efficiency.
Challenge
"High Cost of Advanced Workholding Systems Could Be a Potential Challenge for Consumers"
The cost of AI-integrated with sensor-based workholding solutions acts as a significant obstacle in the implementation of automated and smart future technologies. Manufacturers at the small and medium levels face challenges to afford integration systems that limit them from adopting this technology on a broader scale. Manufacturers must concentrate on designing price-effective modular workholding solutions that are easily upgradable to achieve market penetration success.
WORKHOLDING DEVICES MARKET REGIONAL INSIGHTS
-
North America
North America is the fastest-growing region in this market. The United States workholding devices market has been growing exponentially owing to multiple reasons. The North American workholding devices market is experiencing robust growth because industries actively adopt automated systems and CNC manufacturing methods alongside smart manufacturing. The local automotive aerospace and defense sectors push up the demand for automatic high-precision workholding solutions. The expansion of the market becomes stronger through investments in both Industry 4.0 systems and artificial intelligence applications in manufacturing.
-
Europe
Europe's market for workholding devices expands because all sectors from aerospace to automotive sector and heavy industries need precise machining applications. The workholding innovation market leads through Germany as well as the United Kingdom alongside France. Manufacturers must follow strict regulation standards which drive them to choose eco-friendly and power-efficient workholding solutions.
-
Asia
The workholding devices market in Asia-Pacific expands because of China Japan and India's flourishing manufacturing industries and increasing CNC machine implementations across all sectors along with Asia-Pacific's accelerating industrialization rate. The area attracts business because of affordable production possibilities along with official drives toward automated and smart factory development. The market develops faster because of rising investments in automotive and electronics and aerospace industries.
KEY INDUSTRY PLAYERS
"Key Industry Players Shaping the Market Through Innovation and Market Expansion"
Key industry players are shaping the workholding devices marketplace through strategic innovation and market expansion. These companies are introducing advanced techniques and processes to improve the quality and performance of their offerings. They are also expanding their product lines to include specialized variations, catering to diverse customer preferences. Additionally, they are leveraging digital platforms to increase market reach and enhance distribution efficiency. By investing in research and development, optimizing supply chain operations, and exploring new regional markets, these players are driving growth and setting trends within the workholding devices market.
List Of Top Companies
- LMC Workholding [U.S.]
- Hardinge [U.S.]
- ENERPAC [U.S.]
- Raptor Workholding Products [U.S.]
- SCHUNK [Germany]
KEY INDUSTRY DEVELOPMENT
May 2024: The SOLIDGrip MAXX joined the SOLIDLine family of products at HWR Workholding USA. This device enables clamping of large workpieces while supporting dimensions up to 800 millimeters (31.5 inches). The modular system enables two regular vises to merge into one massive vise by turning them into one structure thereby improving efficiency for large component work.
REPORT COVERAGE
The study offers a detailed SWOT analysis and provides valuable insights into future developments within the market. It explores various factors driving market growth, examining a broad range of market segments and potential applications that may shape its trajectory in the coming years. The analysis considers both current trends and historical milestones to provide a comprehensive understanding of the market dynamics, highlighting potential growth areas.
The workholding devices market is poised for significant growth, driven by evolving consumer preferences, rising demand across various applications, and ongoing innovation in product offerings. Although challenges such as limited raw material availability and higher costs may arise, the market's expansion is supported by increasing interest in specialized solutions and quality improvements. Key industry players are advancing through technological advancements and strategic expansions, enhancing both supply and market reach. As market dynamics shift and demand for diverse options increases, the workholding devices market is expected to thrive, with continuous innovation and broader adoption fueling its future trajectory.
Frequently Asked Questions
-
Which is the leading region in the Workholding devices market?
North America is the prime area for the Workholding devices market owing to its advanced manufacturing technologies and a strong emphasis on automation.
-
What are the driving factors of the Workholding devices market?
Growth in CNC Machining and Automation and Expanding Aerospace and Automotive Industries are some of the driving factors in the Workholding devices market.
-
What are the key Workholding devices market segments?
The key market segmentation, which includes, based on type, the Workholding devices market is Milling/Drilling Workholding, Turning Workholding, Grinding Workholding and EDM Workholding. Based on application, the Workholding devices market is classified as Automotive, Heavy Industrial, Aerospace and Othersses.