Trending Insights
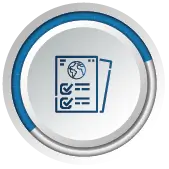
Global Leaders in Strategy and Innovation Rely on Our Expertise to Seize Growth Opportunities
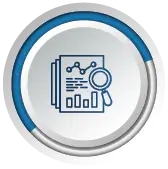
Our Research is the Cornerstone of 1000 Firms to Stay in the Lead
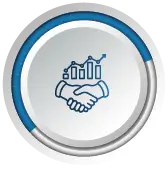
1000 Top Companies Partner with Us to Explore Fresh Revenue Channels
US Tariff Impact on Metal Forging Market
Trump Tariffs Ignite Global Business Evolution
Request FREE sample PDF 
Pharmacy benefit management market
METAL FORGING MARKET OVERVIEW
The global metal forging market was valued at USD 75.77 billion in 2024 and is projected to touch USD 124.28 billion by 2033, exhibiting a CAGR of 5.6% during the forecast period.
Metal forging maintains consistent market expansion as various sectors including automotive aerospace construction and energy sector use such products. The compressive forces used in metal forging result in products that demonstrate both excellent strength and durability. The growing demand for lightweight strong components especially in automotive and aerospace industries enhances the opportunity in forged metal part manufacturing. The market benefits from modern forging technologies through advanced automation systems together with sustainable manufacturing practices that bring improved product performance and lower manufacturing expenses.
The metal forging market finds its main strength in Asia-Pacific because of powerful manufacturing bases operating from China through India to Japan. The region experiences fast industrial growth while its infrastructure development and automotive industries and machinery sector require substantial amounts of forged components which function as primary growth factors. North America along with Europe continues to grow as market segments because of enhanced activities involving high-performance alloys and customized forged component investments. There is projection for sustained metal forging market development and its evolution will be influenced by advancements in smart manufacturing systems and energy-efficient processing methods.
COVID-19 IMPACT
"Metal forging Industry Had a positive Effect as consumer demand for vehicles and air travel increased during COVID-19 Pandemic"
The metal forging market experienced major effects from the COVID-19 pandemic by causing disruptions in supply components and manufacturing activities alongside market demand reductions across industry sectors. The outbreak of COVID-19 caused various forging facilities to operate at partial shutdowns because of lockdown restrictions as well as staff shortages and supply chain complications which slowed their production rates. The metal forging sector confronted reduced market needs because essential industries including automotive, aerospace and construction stopped their operations and experienced travel limitations alongside diminished consumer spending. The market experienced downsizing together with financial difficulties for forging companies across the industry.
The metal forging market demonstrated increased resistance during the recovery period of economies. The automotive together with aerospace sectors began to recover because elevated vehicle and travel consumer interest drove mounting requirements for dependable forged components for high-performance applications. The manufacturing industry adapted to the pandemic by implementing flexible and innovative approaches including digital technology alongside automated systems for upgrading their operational efficiency while eliminating labor dependence. The market experienced short-term obstacles but shows positive long-term development due to growing sector demand and maturing worldwide supply chain stability.
LATEST TREND
"Increasing adoption of additive manufacturing (3D printing) to Drive Market Growth"
The metal forging industry experiences a growing interest toward combining 3D printing technology with conventional forging practices as a modern market trend. The combined manufacturing method enables producers to create intricate parts with better material efficiency and shorter delivery timelines. Business operations benefit from integrating 3D printing at the prototyping stage followed by traditional forging for mass production to reach both precision excellence and component strength improvement and cost savings. The usage of this approach remains common in aerospace and automotive sectors because of their necessity for lightweight high-performance parts. The forging process enables additive manufacturing technology to develop innovative materials as well as customized alloys which satisfy precise engineering needs.
METAL FORGING MARKET SEGMENTATION
By Type
Based on Type, the global market can be categorized into Carbon Steel, Alloy Steel, Aluminum, Magnesium, Stainless Steel, Titanium and Others
- Carbon Steel: Carbon Steel serves as a regular material where iron combines with carbon to provide strength along with durability. The three main applications of carbon steel include construction projects and automotive manufacturing alongside its manufacturing processes because of its low cost and simple workability attributes. Proper treatment is essential for protecting carbon steel from developing corrosion.
- Alloy steels: Alloy steel achieves its superior properties by unifying iron with chromium, nickel and molybdenum along with other metal elements. Due to its enhanced durability and operational endurance as well as resistance against wear and strong resistance properties Alloy steel proves ideal for heavy-duty components such as automotive parts tools and machine components.
- Aluminum: The aerospace industry along with automotive manufacturing and packaging sector rely on aluminum because this lightweight metal shows superior resistance against corrosion. Its lightweight quality with excellent malleability attributes it to critical applications needing reduced weight. The material shows good capability to conduct heat as well as electricity.
- Magnesium: The elemental metal magnesium stands out because it possesses excellent weight strength properties alongside its very light composition. The aerospace and automotive sectors implement this metal for components weight reduction while its corrosion susceptibility surpasses other metallic materials.
- Stainless Steel: The corrosion-resistant metal alloy stainless steel contains iron together with chromium and nickel along with other fundamental components. The material stands out because it shows outstanding durability and exceptional strength alongside resistance to rust and stain formation which makes it perfect for kitchen appliances and medical tools and construction materials.
- Titanium: The strong lightweight metal titanium provides excellent corrosion protection thus making it ideal for aerospace medical and marine components. Its combination of superior strength with minimal weight together with ability to perform under harsh conditions explains why this metal works well for important uses although manufacturers must invest more in procurement compared to standard metals.
By Application
Based on application, the global market can be categorized into Automotive, Defense and Aerospace, Shipbuilding, Power Industry, Oil and Gas, Construction Machinery, Agriculture and Others
- Automotive: In automotive manufacturing metal forging enables the production of tough structural parts which include engine elements and gears and suspension components. Automotive components made through forging operate with enhanced strength-to-weight performance levels thus improving safety measures, fuel economy and performance capability. The automotive industry such as today requires specialized high-precision forged components due to evolving design requirements.
- Defense and Aerospace: Defense and Aerospace sector utilizes metal forging to create essential turbine blades while landing gear and armor are also manufactured through this process. Forged metals maintain exceptional strength together with reliability because they endure demanding operating situations including high temperatures and pressures. Custom products alongside lightweight characteristics and high durability make metal forging desirable for this sector.
- Shipbuilding: The manufacturing process of ships requires forged metal components for building hulls and for creating propellers as well as engines. Forged components positioned in harsh marine environments offer excellent corrosion resistance with strong structure characteristics which make ships durable and reliable. The metal forging process makes it possible to create big powerful components that shipbuilders require for their construction work.
- Power Industry: Metal forging allows the power industry to create turbines and generators and high-stress power production components that play an essential role in the sector. Forged metals keep operating with high strength characteristics while resisting fatigue in applications experiencing both high temperatures and intense pressure. Power generation equipment requires the capacity to craft substantial elaborate product parts.
- Oil and gas: The oil and gas industry depends on forged components to develop drilling equipment together with pipelines along with valves and pressure vessels. The durability and strength that arise from forging help maintain reliable operation of components which work under harsh conditions and high-pressure environments. The success of offshore and deep-sea activities heavily depends on customized forged parts.
- Construction: The production of heavy-duty components including gears axles and structural parts among others occurs through metal forging within construction machinery. The durability of construction equipment operated in harsh settings directly depends on the strength along with wear resistance properties of forged metals. Forged parts play a crucial role in mass production because they deliver high value at reduced prices.
- Agriculture: The production of plows tractors and harvesters for agricultural machinery through metal forging occurs within this domain. Weed parts deliver remarkable strength properties and long-wearing capabilities which make them vital for agricultural equipment due to rigorous loading situations and harsh operating environments. The reliability of forged metals stands as a critical factor which enables farming machinery to operate efficiently throughout its extended service life.
MARKET DYNAMICS
Driving Factors
"Rising Demand for Lightweight and Durable Materials to Boost the Market"
A factor in the metal forging market growth is the Rising Demand for Lightweight and Durable Materials. Multiple industries within automotive along with aerospace and defense require lightweight strong materials to improve their fuel efficiency and reduce emission levels and achieve better performance. Manufacturers utilize metal forging techniques to fabricate parts with superior strength compared to their weight because this enables them to respond to industry requirements especially for automotive systems and aircraft systems along with machinery.
"Increasing Demand from End-Use Industries to Expand the Market"
Integral components used in automotive vehicles aerospace products ship manufacturing and power generator systems come from industries that heavily consume forged materials. The economic recovery worldwide especially following the COVID-19 pandemic has led to rising industrial activity which increases market demand for forged parts with prolonged use and enhanced quality. The automotive industry is intensively investing in forging technologies to make lightweight strong cost-effective components for both electric vehicles (EVs) and standard vehicles.
Restraining Factor
"Complexity and Skill Requirements to Potentially Impede Market Growth"
Businesses require highly qualified personnel with metallurgical and engineering knowledge to perform the technical forging process. The combination of advanced forging process requirements and dependence on qualified experts prevents market expansion in areas lacking suitable personnel training. Manufacturers experience reduced profitability because slower production speeds and higher labor expenses as well as inferior product quality arising from this issue.
Opportunity
"Growing demand for electric vehicle (EV) components To Create Opportunity for the Product in the Market"
Growing market demand for electric vehicle components creates a major business opportunity within the metal forging field. Through the ongoing automotive industry transition to EVs there is elevated demand for forged components used in motor parts as well as chassis and battery housings which need to be lightweight yet durable with high energy efficiency. The market expansion in electric vehicles depends on metal forging technology which provides strength alongside corrosion resistance while reducing weight through its components.
Challenge
"Fluctuation in raw material prices Could Be a Potential Challenge for Consumers"
The metal forging market faces a major operational difficulty because raw material costs tend to change frequently. Controlling raw material prices remains a major challenge in the market because steel and aluminum and titanium undergo price volatility associated with worldwide supply chain problems and geopolitical tensions and economic uncertainty. Forcing companies face profit disturbances and production disruptions in addition to long-term planning challenges because of price instability.
METAL FORGING MARKET REGIONAL INSIGHTS
-
North America
North America is the fastest-growing region in this market. The United States metal forging market has been growing exponentially owing to multiple reasons. The North American metal forging market develops through technological innovation and automation processes. Companies embrace modern forging technologies together with advanced equipment investments to achieve higher efficiency levels and better product quality. The growth in the metal forging industry is supported by two main factors: the rising need for automotive parts that weigh less especially for electric vehicles and the ongoing recovery in aerospace and defense sectors. The area places emphasis on environmental sustainability and its manufacturers are searching for ways to minimize greenhouse gas emissions along with material waste.
-
Europe
The European market of metal forging demonstrates rapid expansion because of development in manufacturing technologies while industries need high-performance components for aerospace and automotive and energy applications. Strong technological innovation in forging methods including precision forging along with additive manufacturing enables producers to make complex durable lightweight parts. The production of electric vehicles together with green energy initiatives creates rising component demand for forged parts which supports industry sustainability goals through regulatory standards.
-
Asia
Fast development of the metal forging market occurs throughout Asia where China India and Japan lead the way because their industries continuously expand their production capabilities and industrial development increases. The area obtains benefits from minimal workforce expenses and supports big manufacturing operations with rising market needs for forged components used especially in automotive vehicles as well as construction projects and energy systems. The metal forging market will experience ongoing expansion due to China and India’s expanding infrastructure development and manufacturing facilities as well as their rising investments in electric vehicles and heavy machinery.
KEY INDUSTRY PLAYERS
"Key Industry Players Shaping the Market Through Innovation and Market Expansion"
Key industry players are shaping the metal forging marketplace through strategic innovation and market expansion. These companies are introducing advanced techniques and processes to improve the quality and performance of their offerings. They are also expanding their product lines to include specialized variations, catering to diverse customer preferences. Additionally, they are leveraging digital platforms to increase market reach and enhance distribution efficiency. By investing in research and development, optimizing supply chain operations, and exploring new regional markets, these players are driving growth and setting trends within the metal forging market.
List of Top Metal Forging Players Profiled
- Precision Castparts Corp. [U.S.]
- Howmet Aerospace Inc. [U.S.]
- Allegheny Technologies Incorporated (ATI) [U.S.]
- Thyssenkrupp [Germany]
- Nippon Steel [Japan]
KEY INDUSTRY DEVELOPMENT
July 2022: Thyssenkrupp engineered special electric vehicle steel gears through their forging process which provided strong performance while decreasing weight. EV drivetrain components utilize these gears because their design enables operation under high torque conditions which supports reductions in energy consumption and extended battery life. The integration of forged steel into vehicle components allows the electric vehicle market to achieve durable and precise system parts while meeting rising sustainability requirements for high-performance components.
REPORT COVERAGE
The study offers a detailed SWOT analysis and provides valuable insights into future developments within the market. It explores various factors driving market growth, examining a broad range of market segments and potential applications that may shape its trajectory in the coming years. The analysis considers both current trends and historical milestones to provide a comprehensive understanding of the market dynamics, highlighting potential growth areas.
The metal forging market is poised for significant growth, driven by evolving consumer preferences, rising demand across various applications, and ongoing innovation in product offerings. Although challenges such as limited raw material availability and higher costs may arise, the market's expansion is supported by increasing interest in specialized solutions and quality improvements. Key industry players are advancing through technological advancements and strategic expansions, enhancing both supply and market reach. As market dynamics shift and demand for diverse options increases, the metal forging market is expected to thrive, with continuous innovation and broader adoption fueling its future trajectory.
REPORT COVERAGE | DETAILS |
---|---|
Market Size Value In |
US$ 75.77 Billion in 2024 |
Market Size Value By |
US$ 124.28 Billion by 2033 |
Growth Rate |
CAGR of 5.6% from 2024 to 2033 |
Forecast Period |
2025-2033 |
Base Year |
2024 |
Historical Data Available |
Yes |
Regional Scope |
Global |
Segments Covered | |
By Type
|
|
By Application
|
Frequently Asked Questions
-
What value is the metal forging market expected to touch by 2033?
The global metal forging market is expected to reach USD 124.28 billion by 2033.
-
What CAGR is the metal forging market expected to exhibit by 2033?
The metal forging market is expected to exhibit a CAGR of 5.6% by 2033.
-
What are the driving factors of the metal forging market?
Increasing Demand from End-Use Industries to boost the market and Rising Demand for Lightweight and Durable Materials to expand the market growth
-
What are the key metal forging market segments?
The key market segmentation, which includes, based on type, Automotive, Defense and Aerospace, Shipbuilding, Power Industry, Oil and Gas, Construction Machinery, Agriculture and Others. Based on application, the metal forging market is classified as Carbon Steel, Alloy Steel, Aluminum, Magnesium, Stainless Steel, Titanium and Others.