Trending Insights
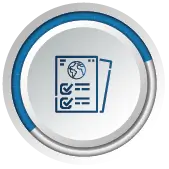
Global Leaders in Strategy and Innovation Rely on Our Expertise to Seize Growth Opportunities
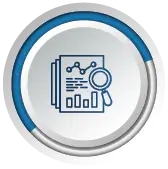
Our Research is the Cornerstone of 1000 Firms to Stay in the Lead
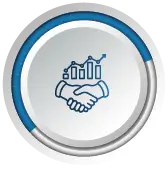
1000 Top Companies Partner with Us to Explore Fresh Revenue Channels
US Tariff Impact on Friction Stir Welder Market
Trump Tariffs Ignite Global Business Evolution
Request FREE sample PDF 
Pharmacy benefit management market
FRICTION STIR WELDER MARKET REPORT OVERVIEW
Global friction stir welder market size was estimated at USD 0.2 billion in 2023, set to expand to USD 0.31 billion by 2032, growing at a CAGR of 5.6% during the forecast period.
A friction stir welder is a sophisticated piece of equipment used in modern welding processes, particularly for joining materials like aluminum and other non-ferrous metals. Unlike traditional welding methods that involve melting the materials being joined, friction stir welding (FSW) creates a solid-state bond. This process is achieved by generating frictional heat and mechanical pressure between the materials, causing them to soften and mix together without reaching the melting point. The friction stir welder consists of a rotating tool with a profiled pin or probe that is plunged into the joint between the materials to be welded. As the tool traverses along the joint line, it creates a high-strength, defect-free weld.
The friction stir welding process offers several advantages over traditional welding techniques. It produces welds with minimal distortion and residual stresses, resulting in improved dimensional stability and structural integrity. Additionally, FSW eliminates the need for consumable filler materials and produces welds with superior mechanical properties, such as higher fatigue resistance and tensile strength. The friction stir welder's precise control over parameters like rotational speed, traverse speed, and downward force allows for consistent weld quality and repeatability, making it a preferred choice for various industries, including aerospace, automotive, shipbuilding, and construction.
COVID-19 Impact: Market Growth Restrained by Pandemic due to Supply Chain Disruptions
The global COVID-19 pandemic has been unprecedented and staggering; with the friction stir welder market experiencing lower-than-anticipated demand across all regions compared to pre-pandemic levels. The sudden market growth reflected by the rise in CAGR is attributable to market’s growth and demand returning to pre-pandemic levels.
The pandemic led to disruptions in global supply chains, affecting the production and distribution of friction stir welding equipment. Restrictions on movement, lockdowns, and temporary closures of manufacturing facilities disrupted the supply of raw materials and components necessary for the production of friction stir welders. Industries such as aerospace, automotive, shipbuilding, and construction, which are significant users of friction stir welding technology, experienced varying degrees of disruption due to the pandemic. Reduced manufacturing activities, project delays, and supply chain constraints in these sectors directly impacted the demand for friction stir welders.
Implementation of social distancing measures, workplace safety protocols, and restrictions on workforce capacity in manufacturing facilities posed operational challenges for friction stir welding equipment manufacturers. These challenges slowed down production processes, leading to delays in fulfilling orders and installations. Economic slowdowns and uncertainty caused by the pandemic led to a decrease in demand for friction stir welding equipment across various industries. Many companies postponed or canceled expansion projects and capital expenditures, leading to reduced investments in welding machinery, including friction stir welders. The market is anticipated to boost the friction stir welder market growth following the pandemic.
LATEST TRENDS
"Advancements in Equipment Technology to Drive Market Growth"
There are ongoing advancements in friction stir welding equipment technology, aimed at improving process efficiency, precision, and reliability. Manufacturers are focusing on developing robotic systems, multi-axis machines, and integrated monitoring and control systems to enhance the capabilities of friction stir welding equipment. The automotive industry continues to adopt friction stir welding for lightweight vehicle manufacturing. This trend is driven by the industry's focus on fuel efficiency and reducing emissions, as friction stir welding enables the joining of lightweight materials like aluminum and composites, resulting in lighter vehicles with improved fuel economy. These latest developments are anticipated to boost the friction stir welder market share.
FRICTION STIR WELDER MARKET SEGMENTATION
- Desktop Welder: A desktop welder is a compact and portable welding machinery designed for smaller-scale welding applications. These welders are typically used for light-duty welding tasks, prototyping, research, and educational purposes. Desktop welders are often preferred for their ease of use, affordability, and suitability for small workshops, laboratories, and hobbyist applications. They are available in various configurations, including manual, semi-automatic, and fully automated models, depending on the specific welding requirements. Desktop welders are suitable for welding various materials such as metals, plastics, and composites, depending on the type of welding process used (e.g., arc welding, laser welding, resistance welding).
- Gantry Welder: A gantry welder is a large-scale welding machine characterized by its gantry structure, which consists of a horizontal beam supported by vertical columns or uprights. These welders are used for heavy-duty welding applications that require high precision, stability, and large working areas. Gantry welders are commonly used in industries such as shipbuilding, aerospace, automotive, construction, and manufacturing, where welding of large structures, components, or assemblies is required. The gantry structure provides stability and rigidity, allowing for precise control of welding parameters and consistent weld quality.
By Application
Based on application the global market can be categorized into Aerospace, Automotive, Shipbuilding, Railways and Others.
- Aerospace: Friction stir welding (FSW) is widely used in the aerospace industry for joining lightweight materials like aluminum and its alloys. Applications include the manufacturing of aircraft fuselage panels, wings, tail sections, structural components, and fuel tanks.
- Automotive: In the automotive industry, friction stir welding is utilized for joining lightweight materials such as aluminum, magnesium, and advanced high-strength steels. Common applications include the fabrication of body panels, chassis components, structural reinforcements, and battery enclosures for electric vehicles (EVs).
- Shipbuilding: Friction stir welding finds applications in shipbuilding for joining aluminum and other non-ferrous alloys used in the construction of ship structures, hulls, decks, and bulkheads. Shipbuilders utilize friction stir welding to achieve high-quality, watertight welds with improved corrosion resistance and mechanical properties compared to traditional welding methods.
- Railways: Friction stir welding is increasingly employed in the railways industry for manufacturing lightweight components, such as aluminum train bodies, floor panels, and structural assemblies. Rail vehicle manufacturers utilize FSW to reduce the overall weight of rolling stock, improve energy efficiency, and enhance performance, particularly in high-speed trains and urban transit systems.
DRIVING FACTORS
"Increasing Demand for Lightweight Materials to Boost the Market"
The growing demand for lightweight materials, such as aluminum and composites, across various industries including automotive, aerospace, and transportation, is a significant driver for the friction stir welder market. Friction stir welding enables the joining of these lightweight materials with high precision and strength, facilitating the development of lighter and more fuel-efficient vehicles and structures. The automotive industry's focus on lightweighting, fuel efficiency, and electric vehicle (EV) manufacturing is driving the adoption of friction stir welding for joining aluminum and other lightweight materials. As automakers seek to reduce vehicle weight to improve fuel economy and range in electric vehicles, friction stir welding emerges as a preferred joining technology for producing lightweight, structurally sound vehicle structures and components.
"Advantages Over Conventional Welding Methods to Expand the Market"
Friction stir welding offers several advantages over conventional welding methods, including reduced distortion, higher joint strength, improved fatigue performance, and the absence of consumable filler materials. These advantages drive the adoption of friction stir welding in industries where high-quality, high-strength welds are critical, such as aerospace, automotive, marine, and construction. Ongoing technological advancements in friction stir welding equipment, including improvements in machine design, tool materials, process control systems, and automation, drive market growth. These advancements enhance the efficiency, reliability, and versatility of friction stir welding processes, making them more attractive to a broader range of industries and applications. These factors are anticipated to drive the friction stir welder market share.
RESTRAINING FACTOR
"Complexity of Process Optimization to Potentially Impede Market Growth"
Optimizing friction stir welding parameters such as tool geometry, rotational speed, traverse speed, and applied force requires expertise and experimentation. Achieving optimal welding conditions for different material combinations, joint configurations, and thicknesses can be time-consuming and challenging, especially for complex or novel applications, which may deter potential users. Although friction stir welding is highly effective for joining certain materials like aluminum and some non-ferrous alloys, its applicability to a broader range of materials is limited. The process may not be suitable for welding materials with large differences in melting points or materials prone to softening or degradation at elevated temperatures, restricting its use in certain applications and industries. The factors are anticipated to hinder the growth of the friction stir welder market growth.
FRICTION STIR WELDER MARKET REGIONAL INSIGHTS
"The market is primarily segmented into Europe, Latin America, Asia Pacific, North America, and Middle East & Africa."
"North America Dominating the Market with Strong Aerospace and Automotive Industries"
North America is home to some of the world's largest aerospace and automotive industries, which are significant users of friction stir welding technology. These industries demand high-quality, high-strength welded components for aircraft, spacecraft, automobiles, and other transportation vehicles. Friction stir welding offers advantages such as lightweighting, improved structural integrity, and enhanced performance, making it a preferred choice for manufacturing critical components in these sectors.
The defense and aerospace sectors in North America are major drivers of friction stir welding demand. Government investments in defense programs, space exploration initiatives, and aerospace research and development contribute to the growth of the friction stir welder market. Friction stir welding technology is extensively used in the aerospace and defense industries for manufacturing structural components, propulsion systems, and other critical parts requiring high-quality welds with minimal distortion and superior mechanical properties.
KEY INDUSTRY PLAYERS
"Key Players Focus on Partnerships to Gain a Competitive Advantage "
Prominent market players are making collaborative efforts by partnering with other companies to stay ahead in the competition. Many companies are also investing in new product launches to expand their product portfolio. Mergers and acquisitions are also among the key strategies used by players to expand their product portfolio.
List of Top Friction Stir Welder Companies
- ESAB [U.S.]
- Grenzebach Maschinenbau GmbH [Germany]
- Nova-Tech Engineering [U.S.]
- Beijing FSW [China]
- FOOKE GmbH [Germany]
INDUSTRIAL DEVELOPMENT
June 2022: The TruLaser Weld 5000 is an advanced friction stir welding (FSW) system manufactured by TRUMPF, a leading provider of industrial laser technology and manufacturing solutions. This product is designed for high-precision and high-efficiency welding of various materials, including aluminum, magnesium, copper, and non-ferrous alloys.
REPORT COVERAGE
The study encompasses a comprehensive SWOT analysis and provides insights into future developments within the market. It examines various factors that contribute to the growth of the market, exploring a wide range of market categories and potential applications that may impact its trajectory in the coming years. The analysis takes into account both current trends and historical turning points, providing a holistic understanding of the market's components and identifying potential areas for growth.
The research report delves into market segmentation, utilizing both qualitative and quantitative research methods to provide a thorough analysis. It also evaluates the impact of financial and strategic perspectives on the market. Furthermore, the report presents national and regional assessments, considering the dominant forces of supply and demand that influence market growth. The competitive landscape is meticulously detailed, including market shares of significant competitors. The report incorporates novel research methodologies and player strategies tailored for the anticipated timeframe. Overall, it offers valuable and comprehensive insights into the market dynamics in a formal and easily understandable manner.
REPORT COVERAGE | DETAILS |
---|---|
Market Size Value In |
US$ 0.2 Billion in 2023 |
Market Size Value By |
US$ 0.31 Billion by 2032 |
Growth Rate |
CAGR of 5.6% from 2023 to 2032 |
Forecast Period |
2024-2032 |
Base Year |
2024 |
Historical Data Available |
Yes |
Regional Scope |
Global |
Segments Covered | |
By Type
|
|
By Application
|
Frequently Asked Questions
-
1. What value is the friction stir welder market expected to touch by 2032?
The global friction stir welder market is expected to reach USD 0.31 billion by 2032.
-
2. What CAGR is the friction stir welder market expected to exhibit by 2032?
The friction stir welder market is expected to exhibit a CAGR of 5.6% by 2032.
-
3. Which are the driving factors of the friction stir welder market?
Advantages Over Conventional Welding Methods and Increasing Demand for Lightweight Materials are some of the driving factors of the market.
-
4. What are the key friction stir welder market segments?
The key market segmentation that you should be aware of, which include, based on type the friction stir welder market is classified as Desktop Welder, Gantry Welder and Others. Based on application the friction stir welder market is classified as Aerospace, Automotive, Shipbuilding, Railways and Others.