Trending Insights
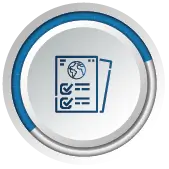
Global Leaders in Strategy and Innovation Rely on Our Expertise to Seize Growth Opportunities
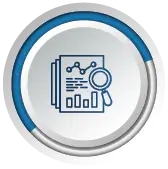
Our Research is the Cornerstone of 1000 Firms to Stay in the Lead
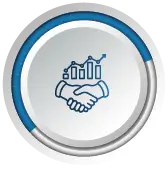
1000 Top Companies Partner with Us to Explore Fresh Revenue Channels
US Tariff Impact on Graphite Machining Center Market
Trump Tariffs Ignite Global Business Evolution
Request FREE sample PDF 
Pharmacy benefit management market
GRAPHITE MACHINING CENTER MARKET REPORT OVERVIEW
The global graphite machining center market stood at USD 1.63 billion in 2024 and is set to rise to USD 1.72 billion in 2025, maintaining a strong growth trajectory to reach USD 2.59 billion by 2033, at a CAGR of 5.4%.
A graphite machining center is a kind of specialized machine tool used for the machining of graphite moulds and these machining centers should generally have high efficient dust cleaning system to handle graphite fine dust. These centers are most crucial in aerospace, automotive, electronics and mould and die industries as they help effectively machine graphite parts for their distinct applications. Machining is preferred over pressing sintering due to the machinability of graphite which enables the free shaping of moulds to meet the production of rods or blocks. The market of these centers can include specific CNC machining centers responding to the most specific properties of the graphite abrasive, high hardness and low thermal conductivity, which guarantee high accuracy and the quality of the parts made of the graphite.
Machining centers are advanced manufacturing tools characterized by relative complexity and enhanced with certain characteristics and possibilities to work with graphite. They incorporate high-speed spindles, precision tools and accurate control systems to get high accuracy in terms of tolerance, fine surface finishes and intricate shapes for graphite products. These capabilities allow manufacturing companies to fabricate different types of graphite parts and products that are important in numerous end-use sectors. These machining centers contribute to yielding efficient and accurate work with graphite through proper fabrication and finishing thus conforming to the high standards set by these industries.
COVID-19 IMPACT
"Pandemic outbreak brings major challenges to the supply chain and the functioning of the market"
The global COVID-19 pandemic has been unprecedented and staggering, with the market experiencing lower-than-anticipated demand across all regions compared to pre-pandemic levels. The sudden market growth reflected by the rise in CAGR is attributable to market’s growth and demand returning to pre-pandemic levels.
The pandemic disrupted the supply chain by imposing lockdowns, travel restrictions and closures of borders that affected the manufacturing process and supply chain vulnerability that graphite machining centers face. These disruptions affected the delivery of key supplies and materials and also disrupted the manufacturing cycle and costs. Due to the limited mobility of commodities and personnel, the supply and demand of graphite machining centers were disrupted. Manufacturers experience problems with inventory control and management of stock with fluctuations in demands from their customers, they also experience problems in delivering products in the required time and offering timely services and maintenance, which impacts the supply chain network.
LATEST TRENDS
"Adoption of more automation and robotics is expected to drive the market growth"
Robots and automation are slowly gaining ground in graphite machining centers and become more popular as they allow the centers to run without operators, work at night or even boost production significantly. This shift is fueled by enhanced automation technology and the expanded Industry 4.0 initiatives, which focus on the introduction and implementation of smart technologies into industrial procedures. These graphite machining centers require the use of robotic arms, sensors and advanced control from artificial intelligence to enable continuous, fast and accurate production without directly involving the human factor. They also lower labour expenses, eliminate weaknesses and enhance the speed and quality of the production process. Automating the process also assists in the ability to operate 24/7 with minimal downtime thus increasing the output and the utilization of resources hence the ability to grow the market.
GRAPHITE MACHINING CENTER MARKET SEGMENTATION
By Type
Based on type the global market can be categorized into Graphite Cutting and High-Speed Graphite Processing Center.
- Graphite Cutting: Graphite cutting centers are most commonly used for cutting and machining graphite. These are specialized equipment that are used to offer high precision in all chosen works to achieve the desired surface finish. These centers are important in industries where graphite parts play a major role such as aerospace and automobile industries. The market is growing due to a high demand for graphite cutting related to the production of lightweight yet strong materials. Recent innovations in technology make graphite cutting centers more efficient and capable of doing more than before.
- High-Speed Graphite Processing Center: The high-speed graphite processing centers try to enhance the rate of production and decrease machining time. They are designed for machining more geometrically intricate products and large numbers of them in a relatively short time. This type of center is very useful in the construction of moulds and electrodes used in Electrical Discharge Machines (EDM). Increased automation promoted by advanced control systems contributes to the efficiency of high-speed graphite processing facilities. Therefore, they are steadily gaining popularity in different sectors of manufacturing industries.
By Application
Based on application the global market can be categorized into Mechinery Industry, Metallurgy and Chemical Industry.
- Machinery Industry: In the machinery industry adopting new, graphite machining centers is crucial for manufacturing high-precision components and electrodes, which require designs and tolerances for moulding and dies. Thus, the requirement for lightweight long-lasting materials creates the necessity for enhanced graphite machining solutions. These technologies increase effectiveness and profitability for various manufacturers, enable compliance with high requirements and guarantee quality and performance in the development of the sector.
- Metallurgy: In metallurgy, these graphic machining centers are important where production is required of electrical and heat conductive parts. They manufacture graphite electrodes that are electromechanical discharge for electrical discharge machining (EDM) used in developing complex metal products. This has made graphite suitable for use in metallurgical operations since it can be machined to accurate dimensions and its wear rate is very low. An increased demand rate and advances in technology machining help to improve these centers, which pull along with them developments in metallurgy.
- Chemical Industry: In the chemical industry, graphite machining centers create application-specific parts such as pumps and valves that with stand severe operating conditions or reactors. Chemical processing can greatly benefit from graphite due to its excellent resistance to corrosion and high temperatures. These centers guarantee accuracy and reliability in performing their tasks, thus meeting the need and expectations of the sector in terms of efficiency and endurance. These essential graphite components are thoroughly tested through advanced analysis, as the industry transitions.
DRIVING FACTORS
"Rising usage of graphite components to open roads for the market"
The demand for graphite components in various industries such as aerospace, automobile, electrical, electronics and renewable energy is highly responsible for the global graphite machining center market growth. Graphite also possesses some features such as high thermal and electrical conductivity, low density, corrosion and high-temperature resistance, which are very useful in those industries. In the aerospace and automotive industries it is used in the molding of intricate machineries and parts hence improving the performance of the industries. In the electronics industry, graphite is used in heat sinks and other thermal management applications while in the renewable energy industry, they are used in battery products and fuel cells. This increased usage makes it a necessity to have machining centers that can machine graphite with higher accuracy and in large quantities. Such specifications necessitate the use of advanced machining technologies for generating high-quality graphite parts to attract the development of the market.
"Requirement for lightweight solutions to increase the market"
The aerospace and automotive industries have continuously been in relentless search of means that would reduce the weight of vehicles for better fuel economy, less emissions and higher performance. Such materials have a graphic intercalation character and are produced for their high strength-to-density ratios and enhanced thermal performance, which makes graphite useful for lightweight load-bearing parts. In aerospace applications, graphite’s strength and heat resistance come in handy when making parts that cannot easily be deformed and offer resistance to heat all while keeping the weight as low as possible. Also, in the automotive industry, the use of lightweight graphite parts increases fuel efficiency or the lowest emissions possible. That is why the focus on the utilization of lightweight materials leads to the growing need for high-performance graphite machining centers to process these materials effectively. High-quality graphite machining solutions remain in demand since industries aim at meeting performance as well as environmental requirements, affecting the market greatly.
RESTRAINING FACTORS
"Tool wear and maintenance increase operating costs and downtime for machining centers posing challenges for the market"
Machining of graphite is intrinsically a highly abrasive operation that results in great levels of tool wear and tool degradation during the machining of graphite parts. This abrasiveness puts pressure on the cutting tools since they wear out very fast, they are changed and maintained from time to time. Due to the loss of coolant, manufacturers are forced to incur additional costs, such as high electricity consumption and long periods of inactivity for machining centers. The constant changing and maintenance of tools contributes a lot to the operating costs and also entails effective control to ensure that the desired degree of machining accuracy is achieved at all times. Moreover, since tools are used for manufacturing, the time used to maintain them can negatively impact production schedules and delivery promises. Mitigating these threats requires purchasing high-durability equipment and adjusting the time intervals to avoid the frequent occurrences of breakdowns, thus improving the dependability of the graphite machining processes.
GRAPHITE MACHINING CENTER MARKET REGIONAL INSIGHTS
"North America due to technological growth and ample investments in machining technologies lead the market"
The market is primarily segregated into Europe, Latin America, Asia Pacific, North America, and Middle East & Africa. North America holds the largest global graphite machining center market share due to its technological advancement and high investments in machining solutions. This regional emphasis on innovation and technology will ensure that a solid framework for the establishment of graphite machining centres is developed. The machining firms in North America use Advanced Machining Technologies (AMT) including automation, robotics and Advanced Control Systems which make them produce quality products with efficiency. Furthermore, improving the capacity in research and development leads to constant advancement in technology in terms of machining and quality graphite components produced. Through this high level of technology integration, robust manufacturing industry and focus on retaining dominance in the industry, North America holds a significant position in the market.
KEY INDUSTRY PLAYERS
"Key Industry players are integrating sustainable strategies to reduce the adverse effects on the environment for market expansion"
The key industry players in the graphite machining center market are implementing sustainability strategies to reduce the impact of emissions on the environment and meet the set standards. Some of these measures include sourcing raw materials that have low energy content and reducing the energy consumed in the manufacturing process and the overall manufacturing cost. They are also concentrating on adopting sustainable materials and processes that helped decrease the amount of emissions that are linked to machining centers manufacturing. Through the improvement of technologies used in manufacturing, especially those being implemented to improve efficiency whilst minimizing wastage, producers are slowly but surely improving their environmental compliance. Moreover, the increased focus on environmental compliance and following high standard environmental requirements is also influencing companies towards integrating these green practices. This commitment to sustainability not only helps in the protection of the environment but also addresses the ever-increasing consumer indulgence and the industrial necessity for environmentally friendly manufacturing solutions.
List of Top Graphite Machining Center Companies
- Sodick (U.S.)
- Makino (Japan)
- OKK (Japan)
- FANUC (Japan)
- Litz Hitech Corp. (Taiwan)
- Takumi (Taiwan)
- Chmer EDM (Taiwan)
- Haiyc (China)
- Prompt (China)
- Yantai Jinpeng Mining Machinery (China)
- SIRIUS ELECTRIC (China)
- Georg Fischer AG (Switzerland)
INDUSTRIAL DEVELOPMENT
September 2023: Erodex UK has announced two new apprentices working at its graphite machining facility in Wednesbury. Jack Needs has joined as an apprentice CNC machinist and Kane Howl is the new apprentice grinder. With over 35 years of experience, Erodex supports the development of future engineering talent by providing on-the-job training combined with further learning from Make UK Apprenticeships. The business is committed to growth by investing in new technology and innovative recruitment techniques.
REPORT COVERAGE
The study encompasses a comprehensive SWOT analysis and provides insights into future developments within the market. It examines various factors that contribute to the growth of the market, exploring a wide range of market categories and potential applications that may impact its trajectory in the coming years. The analysis takes into account both current trends and historical turning points, providing a holistic understanding of the market's components and identifying potential areas for growth.
The research report delves into market segmentation, utilizing both qualitative and quantitative research methods to provide a thorough analysis. It also evaluates the impact of financial and strategic perspectives on the market. Furthermore, the report presents national and regional assessments, considering the dominant forces of supply and demand that influence market growth. The competitive landscape is meticulously detailed, including market shares of significant competitors. The report incorporates novel research methodologies and player strategies tailored for the anticipated timeframe. Overall, it offers valuable and comprehensive insights into the market dynamics in a formal and easily understandable manner.
REPORT COVERAGE | DETAILS |
---|---|
Market Size Value In |
US$ 1.63 Billion in 2024 |
Market Size Value By |
US$ 2.59 Billion by 2033 |
Growth Rate |
CAGR of 5.4% from 2024 to 2033 |
Forecast Period |
2025-2033 |
Base Year |
2024 |
Historical Data Available |
Yes |
Regional Scope |
Global |
Segments Covered | |
By Type
|
|
By Application
|
Frequently Asked Questions
-
What value is the graphite machining center market expected to touch by 2033?
The global graphite machining center market is expected to reach USD 2.59 billion by 2033.
-
What CAGR is the graphite machining center market expected to exhibit by 2033?
The graphite machining center market is expected to exhibit a CAGR of 5.4% by 2033.
-
Which are the driving factors of the graphite machining center market?
Rising usage of graphite components, and requirement for lightweight solutions are some of the driving factors of the market.
-
What are the key graphite machining center market segments?
The key market segmentation that you should be aware of, which include, Based on type the graphite machining center market is classified as Graphite Cutting and High-Speed Graphite Processing Center. Based on application the graphite machining center market is classified as Machinery Industry, Metallurgy and Chemical Industry.